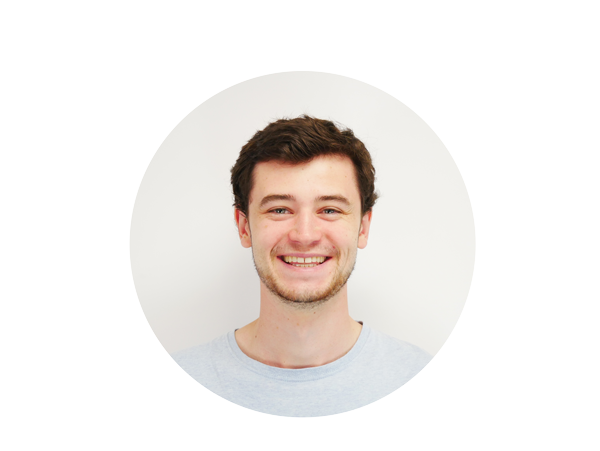
Written by Will Hardy
23/02/2023
TL; DR: We give a short overview of ‘true’ Multimaterial 3D Printing: what it is, its use case and how you can give it a try for yourself.
True Multimaterial 3D Printing: The benefits of combining two or more materials in a single 3D print
Multimaterial 3D printing is the process of combining multiple materials in the same 3D print. It’s a term used across 3D printing disciplines so it can take on a variety of meanings. For FDM it can be taken to mean multiple filaments being used in the same print.
When we say true multimaterial 3D printing, we are alluding to the fact that ‘multimaterial’ is often used to talk about using multiple colours rather than materials. True multimaterial would be two or more materials, say TPU and PLA and not simply a green PLA and a blue PLA.
It’s important to make this distinction. While visually useful, the functional benefits of combining two or more colours are limited but as we will outline in this blog, the benefits of combining two or more materials can be very worthwhile!
Why would I use Multimaterial printing?
Different materials have different properties, and no one material is suitable for every application. Multimaterial prints become especially useful when two potentially opposing properties are required within one part. For example, you need something flexible in one area but rigid in another.
📹 Here’s a great video from Stefan aka CNC Kitchen where he explores combining TPU with PLA using our Toolchanger.
A more mainstream application is for support material, in the form of soluble supports. If you haven’t come across soluble supports, they are often made from PVA (like the glue) and as a result, they dissolve when submerged in water. They are useful when printing very intricate objects where support material would be difficult to remove by hand.
If you don't want to use soluble filament, you could also use one material for the model and another for the supports. PLA and PETG are a good choice as they don’t stick together well and can be easily pulled apart.


📷 PLA with soluble supports and PETG with PLA supports

📷 Using PLA supports for PETG leaves a much smoother surface finish than using PETG supports
How is Multimaterial 3D printing done?
Our previous blog outlined some of the common methods of multimaterial 3D printing. For combining materials rather than just colours, IDEX machines and Toolchanger’s are preferable but other methods can be made to work fairly reliably.
Single Nozzle setups like an MMU (Multi Material Unit) can work fine, but as all the filaments are being fed through the same HotEnd, clogging can occur when switching between materials. This clogging is often caused by a higher-temperature filament not being fully purged and then remaining in the melt zone when the HotEnd temp is lowered. As a result, the higher temp filament doesn’t melt properly and blocks off the nozzle.
By using A ToolChanger or IDEX machine, you have separate filament paths for each material which eliminates the chance of a clog or blockage being caused by swapping filaments mid print.
How to try it for yourself without a multimaterial capable printer
If you want to give it a try, but don’t have access to one of the above methods, this model by ‘Rainer’ on Printables combines PLA and TPU. You don’t need a multimaterial setup for this one as it’s carefully designed to use manual filament swaps. In fact, to improve the bond between PLA and TPU, the design carefully creates interface layers between the two materials.
📹 Here’s a great video from Rainer Schlosshan where he explores combining TPU with PLA without a multimaterial-ready printer.
Why using interface layers between materials can be important
Some materials stick together better than others, but even for those materials that do stick together, the layer-to-layer bond between them can often be weak. For example, PLA and TPU are a good match as they will stick together easily. However, the bond between two layers of PLA will be considerably stronger than the bond between one layer of PLA and one of TPU.
By interfacing the layers, you can artificially improve this connection as seen in the example print above. You can also improve the connection by increasing the contacting surface area between the two layers. For more information on this method, you should check out Rainer's Blog.
For some applications, this extra strength may be unnecessary, but if your part is going to be under any sort of load or strain, it’s worth considering.
Cura takes this a step further with built-in material interlocking feature
In Ultimaker Cura 5.3 beta, multimaterial interlocking has just been introduced. It can be done on any printer capable of printing with two or more materials and is achieved by creating a physical pattern between the two materials, locking them in place. In theory, it works with any two materials regardless of whether they stick together. This is a really helpful innovation and thanks to Cura being open source, it will no doubt, be integrated into other slicers in the coming months too.


📷 An example of Cura's material interlocking in use. Image source.
To conclude
Multimaterial 3D printing, is still very much in its infancy. With advancements in more novel areas of the FDM industry such as Toolchanging 3D printing, non-planar 3D printing and even in 4D printing (– yes, that’s a thing!), we can expect to see some progression in multimaterial too. The slicer integration should see further development, which in turn should help to make it more accessible to the end user.